Углеводородное волокно — что это, характеристики, свойства, производство
Углепластик (карбон) имеет невероятно широкую сферу применения. Углеродные материалы и изделия из них можно встретить в самых разнообразных отраслях промышленности.
В строительстве, например, углеродные ткани применяются в Системе внешнего армирования. Использование углеродной ткани и эпоксидного связующего при ремонте несущих конструкций (мостов, промышленных, складских, жилых зданий) позволяет проводить реконструкцию в сжатые сроки и со значительно меньшими трудозатратами по сравнению с традиционными способами. При этом, хотя срок ремонта снижается в разы, срок службы конструкции увеличивается также в несколько раз. Несущая способность конструкции не просто восстанавливается, но и увеличивается в несколько раз.
В авиации углеродные материалы используются для создания цельных композитных деталей. Сочетание легкости и прочности получаемых изделий позволяет заменить алюминиевые сплавы углепластиковыми.
В атомной промышленности углепластики используются при создании энергетических реакторов, где основным требованием к используемым материалам является их стойкость к высоким температурам, высокому давлению и радиационная стойкость. Кроме этого, в атомной отрасли особое внимание отдается общей прочности внешних конструкций, поэтому Система внешнего армирования также имеет обширное применение.
В автомобилестроении карбон (или углепластик) используется для производства как отдельных деталей и узлов, так и для автомобильных корпусов целиком. Высокое отношение прочности к весу позволяет создавать безопасные, и в то же время экономичные автомобили: снижение веса автомобиля за счет углепластиков на 30 % позволяет снизить выброс CO2 в атмосферу на 16% (!), благодаря снижению расхода топлива в несколько раз.
В гражданской аэрокосмической отрасти композиционные материалы занимают очень прочные позиции. Высокие нагрузки космических полетов ставят соответствующие требования и материалам, которые используются при производстве деталей и узлов. Углеродные волокна и материалы из них, а также из карбидов работают в условиях высоких температур и давления, при высоких вибрационных нагрузках, низких температурах космического пространства, в вакууме, в условиях радиационного воздействия, а также воздействия микрочастиц и т.п.
В судостроении высокая удельная прочность, коррозионная стойкость, низкая теплопроводность, немагнитность и высокая ударостойкость делают углепластики лучшим материалом для проектирования и создания новых материалов и конструкций из них. Возможность сочетать в одном материале высокую прочность и химическую инертность, а также вибро-, звуко- и радиопоглощение обуславливает выбор именно этого материала для изготовления конструкций различных видов гражданских судов.
Одной из наиболее значимых областей применения углеродных материалов в мировой практике является ветроэнергетика. В нашей стране эта отрасль находится, по сути, в стадии зарождения, в то время как во всем мире ветряки появляются и в незаселенных районах, и в прибрежных зонах, и на морских платформах. Легкость и непревзойденные показатели прочности на изгиб углепластиков позволяют создавать более длинные лопасти, которые, в свою очередь, обладают большей энергопроизводительностью.
В железнодорожной отрасли углепластики имеют широкое применение. Легкость и прочность материала позволяет облегчить конструкцию железнодорожных вагонов, снизив тем самым общий вес составов, что позволяет в дальнейшем как увеличивать их длину, так и улучшать скоростные характеристики. В то же время углепластики могут использоваться и при строительстве железнодорожного полотна и прокладке железнодорожных проводов: высокие показатели прочности на изгиб позволяют увеличивать длину проводов, сокращая необходимое количество опор и в то же время снижая риск их провисания.
Композиционные материалы интенсивно входят в привычный мир каждого человека. Из них создаются многие товары народного потребления: предметы интерьера, детали бытовых приборов, спортивная экипировка и инвентарь, детали ЭВМ и многое другое.
Почему карбон не используется в массовом автопроме — Автомобили
Карбон – народное название, транслитерированное с английского слова carbon – уголь, которое в свою очередь было заимствовано еще из латыни. Углепластик представляет собой полимерный композиционный материал, состоящий из нитей углеродного волокна, переплетенных под определенным углом — как шерсть в свитере. Только очень прочный, с высокой степенью натяжения, низким весом и низким температурным расширением. Из-за его дороговизны композит может применяться как усиливающее дополнение, например, к стали — тогда материал получит приписку «усиленно углепластиком», CFRP.
Зона применения
Свою блистательную карьеру карбон начал с ракетных двигателей, а сегодня применяется в самых различных сферах — от производства удочек до самолетостроения. И в автопромышленности — не в последнюю очередь, прежде всего, в структуре кузова, а также элементах отделки экстерьера и интерьера.
Углепластик хорош тем, что обладает высокой прочностью, жесткостью и малой массой — он прочнее алюминия и легче стали, оказываясь более эффективным материалом. У кузова, изготовленного с применением композита, больше жесткость на кручение, что играет на руку безопасности автомобиля, и выше стойкость к коррозии. Даже применение части карбоновых деталей, даже только в отделке интерьера, снижает массу автомобиля, а значит, повышает топливную экономичность и динамические характеристики. При массовом применении повысилась бы и общая безопасность на дорогах при авариях, а также безопасность пешеходов.
Да и просто карбон считается красивым и стильным материалом — ведь спросом пользуется даже имитация «под карбон», которую с удовольствием используют в деталях и интерьере недешевых машин. Что уж говорить о пленке «под карбон», которая не добавляет кузову ни прочности, ни легковесности.
Однако из-за своей дороговизны углепластик далек от рынка массовых автомобилей и используется только в эксклюзивных дорогостоящих моделях, а также автоспорте. Но почему этот материал в прямом смысле «на вес золота»?
Дорогое производство
Окончательный ценник автомобиля в автосалоне складывается из сотни факторов: необходимость окупить затраты на создание идеи и разработку проекта, зарплаты дизайнеров и маркетологов, стоимость рекламы и имидж бренда. И мы можем только догадываться, насколько отличается себестоимость автомобиля от его покупательской цены.
Затраты на производство кузова с применением углепластика, его обработка и сборка мало чем отличаются от той же стали. Однако причина дороговизны композитной автомобильной детали объективна — дорог сам материал. Стоимость сырья составляет 20 долларов за килограмм, в то время как килограмм стали обойдется менее чем в один доллар.
Во-первых, из-за высокого спроса (например, из-за широкого применения в самолетостроении) на рынке наблюдается дефицит волокна, что также играет на его подорожание.
Во-вторых, сам процесс производства углеволокна очень трудоемкий и дорогостоящий. Итак, начинается все еще с нитей, из которых «вяжется» карбоновая пластина. Углеродные волокна получают за счет термической обработки химических и природных органических волокон, при которой в материале волокна остаются главным образом атомы углерода. Сначала происходит окисление исходного волокна – на воздухе при температуре 250 градусов Цельсия в течение 24 часов, потом стадия карбонизации — нагрев волокна в среде азота или аргона при температуре от 800 до 1500 градусов Цельсия, а затем графитизация в инертной среде при температуре 1600-3000 градусов. В результате количество углерода в волокне доводится до 99%.
И на выходе одно только стартовое сырье становится в два раза дороже, чем исходный материал, так как половина элементов просто сгорает. Не считая расходов на специализированное оборудование и затрачиваемую энергию — представьте, сколько это стоит при обработке в перечисленных выше условиях и температурах, да и сами автоклавы (оборудование) значительно дороже. Более того, нужно избавиться от исключенных элементов, а утилизация этих «отходов производства», не вредящая окружающей среде, еще один важный пункт в счете расходов.
И это мы только сделали нити, а ведь из них еще надо «сплести полотно», которое и будет обладать той удивительной прочностью. И прежде всего, придется убедиться, что все нити одинаковы и равномерно растягиваются, иначе в полотне какие-то из них будут более уязвимы, а следовательно, сломаются. Так что необходимы сложные и дорогостоящие меры контроля качества изделий — в случае ошибки при производстве материал окажется хрупким, а не суперпрочным.
Затем нити работают с термоактивными смолами, которые их «склеивают», в результате и получается композит. Эти смолы также дороже обычных. А ведь композиту еще нужно придать форму, что занимает около часа — очень долго, если сравнивать с тем, как быстро штампуются кузовные панели из стали. Деталь из углепластика производится двумя способами. При прессовании углеткань выстилается в форму, смазанную антиадгезивом (например, мылом), пропитывается смолой, излишки смолы удаляются в ваккуме или под давлением, смола полимеризуется. Второй вариант — контактное формование: берется исходная деталь (например, металлический бампер), смазывается разделительным слоем, сверху напыляется монтажная пена. После затвердевания слепок смазывают разделительным слоем и выкладывают пропитанную углеткань, которая прокатывается, полимеризуется и затем снимается.
И наконец карбон, несмотря на свою прочность, уязвим для точечных ударов, а треснувший углепластик плохо пригоден к ремонту. Невидимые глазу внутренние трещины и расслоения приводят к снижению плотности. Скорее всего, поврежденную композитную деталь автомобиля придется заменять.
Вот что рассказал порталу «АвтоВзгляд» директор по послепродажному обслуживанию «Ауди Центр Восток» Алексей Кирдяшов:
— Высокая стоимость углепластика объясняется в первую очередь тем, что для изготовления карбона требуются высококачественные дорогостоящие компоненты и используется сложный процесс производства. На цену материала также влияют его уникальные характеристики — прочность и легкость. Это естественно, что за такое «ноу-хау» и эксклюзивные свойства продукта производители делают наценку, объясняя это тем, что карбон — будущее в автомобилестроении, авиастроении, изготовлении электроники, строительстве и многом другом. Продукт пользуется спросом, но еще не используется массово из-за своей стоимости…
Путь к удешевлению
Но коль дорого стоит производство, а не сам «алмаз», то его можно удешевить, упростив и удешевив технологию получения углеволокна. И, судя по последним заявлениям, производители композитов уже близки к этому. Ради совершенствования технологий производства карбона создан специальный немецкий проект MAI Carbon, на который работает более 70 компаний, институтов и лабораторий, в том числе Audi и BMW. И по словам его руководителя Клауса Дрекслера, затраты на производство углеволокна могут быть снижены на 90%. В результате композит может стать значительно дешевле, а значит, доступным для массового автомобильного производства. А при увеличении объемов производства кузова из углепластика станут стоить столько же, сколько стальные, и появятся у дешевых автомобилей.
По словам Дрекслера, для удешевления и ускорения производства нужно сделать процесс более автоматизированным. Подробностей участники проекта пока не раскрывают, однако в качестве реального примера можно вспомнить литиевые батареи, которые в последние годы удается делать все более доступными. Пассажирская клетка электрокара BMW i3 выполнена из композита, а ведь это уже массовая модель.
Например, технология струйного переноса сухой смолы, разработанная и запатентованная австралийской компанией Quickstep на средства правительства, уже позволяет автоматизировать изготовление кузовных панелей. Робот распыляет смолу особого состава в сухом виде, что позволяет избавиться от дорогостоящей подготовки жидкой смолы. Анализируется применение в качестве карбонового сырья лигнина, который получают из древесины и который по прочности на сжатие соответствует бетону, или подогрев при помощи плазмы. Ищут способы заставить углепластик работать с термопластиковыми смолами, что может удешевить производство на 60-70% и упростить устранение ошибок.
Похоже, революция на пороге.
Карбоновые удилища. Вся правда о карбоне
В последнее время, как только заходит речь об удилищах, сразу же вспоминают про различные аббревиатуры, которые характеризуют карбон, из которого сделаны удилища. 1К, 2К, 3К. «Это удилище из высокотехнологичного карбона», «Высококачественный карбон, делает удилище..», «Карбон, из которого сделан бланк, отвечает самым высоким требованиям» и так далее, и так далее. А что же скрывается за всей этой маркетинговой терминологией?
Что такое карбон?
Карбон — углерод, представляющий собой полимерный композиционные материал из переплетенных нитей углеродного волокна, расположенных в матрице из полимерных смол. Отличается высоко прочностью и малой массой. Зачастую гораздо прочнее стали, но в разы легче. По удельным характеристикам превосходит многие высокопрочные стали.
Но отойдем в сторону от точных определений. Самое главное, что вы должны понимать в карбоне, что его на самом деле существует два вида: чистое углеродное волокно (оно же carbon fiber) и углепластик (полимер, усиленный углеродным волокном — carbon fiber reinforced polymer). Оба этих материала в быту называют карбоном, что, в конечном итоге, привело к тому, что понятия стали путать между собой.
Практически весь карбон, из которого делаются удилища получается из полиакрилонитрила (сокращенно ПАН) при помощи окислительного пиролиза и последующей обработки в инертном газе. Нити углерода получаются очень тонкие (ориентировочно 0,005-0,10мм в диаметре), сломать их очень просто, а вот порвать очень сложно. Из этих нитей и сплетаются ткани, из которых затем делаются бланки для удилищ.
Почему карбон так удобен для производстве удилищ?
Использование карбона позволяет достигнуть высокой прочности удилища, жесткости, при очень малом весе. Дело в том, что карбон является материалом, механические свойства которого зависят от направления волокон. Комбинируя их в различных направлениях, можно добиваться оптимальных характеристик различных изделий, будь то удилища или любое другой изделие. То есть, характеристики бланка зависят напрямую от того плетения, на которое пал выбор разработчиков удилища. Карбон позволяет добиться практически любой формы изделия, именно поэтому у инженеров куда больше возможностей и свободы в создании «идеального» удилища.
Из какого карбона лучше всего покупать удилища?
Это очень сложный вопрос. Определить на глазок что за карбон перед вами очень тяжело. Производители могут написать всякое. Единственный совет, который точно можно дать — это избегать различных дешевых «трехкопеечных» бланков непонятного производства. Остается только гадать откуда производитель берет этот материал. А самое главное, большинство рецептов карбонового волокна являются частной собственностью (запатентованными) и просто так ни одна фирма не расскажет вам состав.
Точно так же не стоит доверять различным рекламным лозунгам, что такая-то компания использует «особенный», «исключительный», «высокотехнологичный» и так далее карбон. Правда состоит в том, что две трети мирового рынка по производству карбона принадлежат трем японским фирмам — Toray (30%), Mitsubishi (18%), Toho (18%). За ними расположились такие фирмы, как венгерская Zoltek (17%), немецкая Hexcel (7%), американская Cytek (3%), на всех остальных приходится в общей сложности еще 6%.
Всего в год производится порядка 43,5 тысяч тонн карбона. Из них 41% — потребляет авиация, космическая и военные промышленности. 17% — спорт, 12% — строительство 12% — различные нужды, по 5%-6% автомобилестроение, гражданская инженерия и так далее. Не будем тонуть в цифрах.
Важно, что из всего оборота на спорт, рыбалка забирает не более 2-3%. Теперь вдумайтесь — если вы владеете инфраструктурой, позволяющей исследовать новые виды карбоновых волокон, чем вы займетесь — производством деталей для космической промышленности или для удилищ? Будете работать с 41% рынка или сосредоточитесь на двух процентах даже не от общего рынка, а от 1/5 этого рынка? Ответ очевиден, поэтому искренность заявлений производителей рыболовных аксессуаров касательно «уникального карбона» вызывает большие подозрения. Мы не беремся утверждать, правда это или нет. Мы просто даем пищу для размышлений.
Характеристики карбона
При получении карбона из поликарилонитрила, под микроскопом полученная нить будет напоминать ствол дерева. Плотный в центре, с шероховатой корой снаружи. Если продолжать очищать нить от «коры», то получится нить меньшего диаметра, но большей плотности. Соответственно на одну и ту же единицу площади поместится большее количество таких нитей, что позволит добиться не меньшей жесткости, но гораздо уменьшить вес. Производство таких тонких волокон сопряжено с большими издержками, потому что волокно получается хрупким и использовать его необходимо с большой осторожностью.
Отсюда и высокая стоимость такого карбона. Однако очень эластичный карбон является очень хрупким материалом. Поэтому инженером постоянно приходится ломать голову, чтобы найти оптимальный баланс между прочностью и эластичностью. Это достигается уже при помощи рецепта карбонового волокна, в котором комбинируют несколько слоев карбона с различными характеристиками. Каждая такая комбинация и есть главная тайна и секрет любого удилища, да и просто изделия.
Теперь стоит поговорить о самых наших любимых характеристиках — 1К, 2К, 3К, которыми часто маркируют карбон. Подобная маркировка относится к плетению углеродного волокна. Нити собирают в полоски и эти полоски переплетают друг с другом. 1К означает, что в полосе 1000 нитей, 2К — 2000 нитей, а 3К — 3000 нитей. На самом деле эта характеристика никаким образом не является признаком тех или иных свойств самого волокна. Важно не количество нитей в полосе, а то, каким образом плетутся эти полосы, и из какого состава-рецепта сделаны волокна. А это уже зависит от производителя.
Вернемся к мировому рыболовному рынку!
Здесь все сурово. Подавляющее большинство удилищ, которые сегодня продаются в магазинах изготовлены в Азии, на фабриках, каждая из которых обслуживает сразу несколько брендов. Современные бренды, причем не только в рыболовной индустрии, в большинстве своем являются самыми настоящими маркетинговыми и инженерными центрами, но не производителями.
Они заключает контракты с так называемыми Original Equipment Manufactures, если говорить по-русски, посредниками, отсылают им дизайн и желаемые характеристики, которые они хотят получить на выходе, а уже OEM несет ответственность за производство. Такие фабрики отправляют готовые удилища, на которых стоит Made in China, или же могут отправить удилище, которое будет еще доведено до ума. Во втором случае вы можете зачастую видеть заветные Made in UK, Made in Germany и так далее.
Вполне распространенная практика, когда сразу несколько компаний работает с одной и той же фабрикой. Но также и бывает масса случаев, когда один бренд работает с несколькими OEM, когда хочет производить несколько видов удилищ.
Но это вовсе не означает, что вас обманывают. Как раз нет. Ведущие бренды отдают процесс производства карбоновых удилищ в руки профессионалов, которые занимаются только плетением карбоновых волокон и изделиями из карбона. Конечно, это все стоит денег, и увеличивает цену исходного продукта. Теперь представим ситуацию, когда вы покупаете вроде бы карбоновое удилище, которое стоит ну совсем дешево.
Сразу можете убрать отсюда работы по инженерным расчетам и дизайнеров. Вам просто продают готовую, стандартную заготовку, уберите затраты на маркетинговые исследования и сертификацию производства (самый главный признак отсутствия контроля качества) и так далее.
Репутационные риски заставляют известные бренды подходит крайне ответственно к вопросу качества, тогда как никому неизвестные производители подобных рисков вообще не имеют. Ну закрыл ты эту фирму, открыл завтра новую. Вот и все дела. Вы никогда не узнаете какие конкретно материалы были использованы, какая смола, что ожидать от удилища. Если вы считаете данный риск оправданным низкой ценой, конечно, покупайте. Но разве много у нас людей осознают эти риски? Надеемся, что после прочтения данной статьи, их число хотя бы немножко увеличится.
Полное или частичное копирование без согласования с редакцией портала запрещено
Карбон — премиальный материал для рукояток ножей
Одним из самых престижных и дорогих материалов для рукояток ножей помимо титана и дорогостоящих пород древесины, является разновидность углепластика, так называемый «карбон». Материал ценится за исключительную легкость, прочность и эстетическую красоту.
Источник фото: https://ua-marine.com.ua/katalog/tkani-i-vinili-vyva/vinili-vyva/carbon-fiber/
Карбон (от англ. carbon — углерод) — это полимерный материал с композитным составом, изготовленный из переплетенных нитей углеродного волокна (сarbon fibers). Эти нити изготавливаются с использованием эпоксидных смол. Средняя плотность материала от 1450 кг/м³ до 2000 кг/м³. Главным отличием карбона от других полимеров применяемых при изготовлении ножей является очень небольшой вес. Именно вес в совокупности с исключительной прочностью дает карбону преимущество перед другими материалами рукояток: полимером G10, микартой, пластиком FRN и т.д. При этом по удельным характеристикам прочности карбон превосходит конструкционные стали. Основными качествами карбона являются: высокая прочность на разрыв, стойкость к высоким температурам, агрессивным средам, незначительное расширение при нагреве, высокая электропроводимость.

Источник фото: http://surl.li/wdqi
Основу материала составляют нити углеродистого волокна, средней толщиной 0,005-0,010 мм в диаметре. Углеродные волокна изготавливаются в результате сложного процесса термообработки. Основное волокно (полиакрил, вискоза) изначально подвергается окислению на воздухе при температуре 250 °C в течение 24 часов. В результате окисления образуются лестничные структуры (полимеры, макромолекулы которых попарно сшиты регулярными химическими связями). Затем происходит карбонизация (процесс обогащения нитей углеродом), который проходит при нагреве волокна в среде азота или аргона при температурах от 800 до 1500 °C. В результате карбонизации происходит образование графитоподобных структур (аллотропных модификаций углерода). Процесс термической обработки заканчивается графитизацией (образованием графита в материалах, в которых углерод содержится в растворенном состоянии или в виде карбидов), она проходит при температуре 1600-3000 °C, в инертной среде.
Источник фото: http://svouimirukami.ru/articles/uglerodnoe-volokno-chto-eto-takoe-primenenie-karbona-v-sovremennom-…
Углеродные ткани в свою очередь получают путем плетения нитей или лент. При производстве этих нитей за основу взят углеродный ровинг — жгут из тонких непрерывных нитей углеродного волокна толщиной от 3-х микрон, образованных атомами углерода. После переплетения они составляют каркас углепластика. Количество углеродного волокна в нити оценивается числом «К» — количеством тысяч элементарных углеродных волокон. Самое тонкое и самое дорогое углеродное волокно — 1К, наиболее распространенное углеродное волокно 3К, существуют также нити из углеродного волокна с К = 6, 12, 24, 48. Ткань, изготовленная из нитей, может иметь разнообразный рисунок плетения (ёлочка, рогожа, саржевое плетение и др.
Источник фото: https://compoly.ru/produktsiya/uglerodnye-pan-materialy/uglerodnaya-tkan.html
Основными методами изготовления карбоновых пластин являются:
Прессование, при котором ткань выстилается в форму, предварительно смазанную так называемым антиадгезивом, предназначенным для уменьшения сцепления поверхностей друг с другом. Им может мыло, воск и т.д. Затем ткань пропитывается смолой, а излишки смолы удаляются в вакууме (вакуум-формование) или под давлением. После полимеризации, смолы изделие приобретает законченный вид.
Вакуумная инфузия, позволяет создавать ламинатный пакет наложением слоев ткани друг на друга и под слои подается вакуумное разряжение. Затем через клапан подается связующие вещество и под действием вакуума оно заполняет пустоты и пропитывает углеродную ткань.
Вакуумное формование, представляет собой склеивание слоев при высоких температурах и затем воздействие вакуумом для формирования объема изделия. Этот способ является одним из самых дешевых.
Метод намотки, который заключается в наматывании пропитанного ровинга на предварительно подготовленную форму. После намотки нужного числа слоев, форма с намотанной тканью помещается в нагревательную печь и полимеризуется.
Метод SMC/BMC
заключается в помещении ткани в пресс-форму, нагретую до рабочей температуры. Пресс-форма смыкается, в результате чего под давлением материал растекается в полости формы и затвердевает. В конце цикла изделие извлекается из пресс-формы, и производится его окончательная механическая обработка и окраска.
Источник фото: https://www.zr.ru/content/news/538358-bmw_vstupajet_v_eru_avtomobilej_iz_karbona/
Карбоновое волокно применяется в различных сферах. В частности, в авиа и ракетостроении, при производстве деталей корпуса автомобилей и мотоциклов, бытовой техники и высокотехнологичных исследовательских приборов. И уже порядка 20 лет карбон широко применяется в изготовлении рукояток ножей среднего и премиального сегмента. При этом на складных ножах карбон может быть как в виде накладок на стальные лайнеры, так и в виде единственного материала рукояти, закрепленного винтами через бонки.
Карбон, идущий на изготовление ножей, помимо своих основных прочностных характеристик, должен иметь еще и достаточно привлекательный внешний вид. Именно этот фактор увеличивает его стоимость, осложняя технологию производства и требуя самых качественных исходных материалов. Для проклейки слоёв используются самые дорогие и качественные смолы, и более дорогое оборудование, в частности химические реакторы (автоклавы). Кроме того, для повышения сцепления с рукой карбон подвергают пескоструйной обработке, что также увеличивает затраты на производство. Необходимо также помнить, что работа с карбоном требует обязательной защиты органов дыхания и специальных помещений с хорошей вентиляцией, и это также ведет к росту цены.
Цветовая палитра и текстура карбона, используемого на ножах, может быть разнообразной. Среди разновидностей карбона применяются:
Мозаичный карбон, который может быть как однотонным, так и разноцветным. Такой карбон применяется для радиусных проставок на ножах со сложными многосекционными рукоятками. В данном карбоне могут применяется несколько технологий окрашивания.
Источник фото:https://drwinter-knives.livejournal.com/285748.html
Мраморный карбон — представляет собой хаотичное сплетение карбоновых нитей, каждая из которых по-разному отражает свет, что дает ему возможность блестеть под разными углами обзора.
Источник фото: https://guns.allzip.org/topic/189/2411436.html
Карбон Lightning Strike («удар молнии») с медной нитью в виде сетки, вплетённой в углеткань по всему её объёму. Внешне аналогичный применяемому в фюзеляжах американских самолетов для защиты от ударов молний. Это тонкий карбон, толщиной 3,2 мм саржевого плетения. Обладает глубоким и ярким рисунком.
Источник фото:http://knife-making.ru/index.php?route=product/product&product_id=1475
Как и любой дорогостоящий, и при этом сложный в изготовлении материал, карбон имеет ряд недостатков. При производстве углепластиков необходимо очень строго выдерживать технологические параметры, при нарушении которых прочностные свойства изделий резко снижаются. Для контроля качества изделий могут применяться ультразвуковая дефектоскопия, рентгеновская и оптическая голография, а также акустический контроль. Без них производитель работает «наощупь» и может не заметить скрытых дефектов. Другим серьёзным недостатком углепластиков является их низкая стойкость по отношению к ударным нагрузкам. Также необходимо помнить, что со временем карбон выцветает и может существенно терять свое главное преимущество – привлекательный внешний вид. Однако несмотря на эти недостатки карбон по праву является премиальным материалом для лучших ножей.
Придет ли углепластик на массовую стройку
Прошел год с момента подписания Дмитрием Медведевым правительственного распоряжения № 1307-р от 24 июля 2013 года об утверждении плана мероприятий «Развитие отрасли производства композитных материалов». Тогда же министр регионального развития Игорь Слюняев приказом № 306 в соответствии с поручением Президента от 12 ноября 2012 года утвердил отраслевую программу внедрения композиционных материалов, конструкций и изделий из них в строительном комплексе России. Что делается и что еще предстоит сделать в этом плане?
Что это такое
Сам факт того, что слово «композит» сегодня звучит на самом высоком уровне, является показателем обеспокоенности руководства страны состоянием этого сегмента стройиндустрии. Ведь уровень применения современных композиционных материалов в производстве — один из критериев, по которому оценивается степень развития страны в целом. А нынешние меры, предпринимаемые Западом для изоляции России, еще сильнее выявляют проблемы нашей зависимости от импорта, в том числе от составляющих для изготовления композиционных материалов.
Под термином «композит» сегодня понимают современный материал, состоящий из полимерной (керамической, металлической, углеродной или другой) основы, армированной наполнителями. В качестве последних также используют разные материалы, из которых наиболее широко распространены стекло-, базальто- и углеволокно, а также сплетенные из них холсты.
А что же карбон, он же углепластик? Это продукт высоких технологий — композиционный материал, где наполнителем служит углеродное волокно или ткань, а связующим (матрицей) является полимер (например, эпоксидная смола), который затвердевает при определенных условиях. У разных полимеров — разные условия отверждения: повышение температуры, наличие катализаторов, специальных отвердителей и пр.
Волокна в углепластике — ?5-10 мкм и состоят из цепочек атомов углерода, выстроенных в кристаллическую решетку. Жгуты из таких волокон имеют очень высокое сопротивление на растяжение. Так, прочность на разрыв у углеволокна в четыре раза выше, чем у лучших марок стали. При этом его плотность вчетверо меньше. Опыт показывает, что порвать тонкий стержень из углепластика ?5 мм можно только при нагрузке 2,5 тонны. Для сравнения: образец из чугуна таких же размеров рвется уже при 150 кг.
В поперечном направлении волокна углерода имеют существенно меньшую прочность, поэтому чтобы реализовать прочностные характеристики волокон в изделии, нужно располагать их в матрице, ориентируя в нужных направлениях. Фактически затвердевший массив матрицы и компенсирует недостаток прочности волокон в их поперечном направлении. Как его получают Процесс получения углеволокна весьма энергоемок. Графитовые нити получают в несколько этапов при нагреве вискозных или полиакрилонитрильных (ПАН) волокон в разных средах. Органические нити доводятся до стадии обугливания, в результате чего и появляется материал из чистого углерода. Поэтому конечный продукт выходит весьма дорогим.
Точно так же существуют и разные технологии получения углепластиков, которые отличаются формой, размерами и свойствами изделий — весом, прочностью, огнестойкостью и пр. Это могут быть ленты и полотна из углеволокна, которые пропитывают на объекте эпоксидной смолой. Готовые профили для конструкций мостов или прутки арматуры, в которых нити наполнителя «замоноличены» затвердевшим полимером. Изготавливают и так называемые препреги — полотна углеволокна, заранее пропитанные смолами, из которых в заводских условиях при высоких температуре и давлении формуют готовые детали.
Кстати, именно такие изделия востребованы в авиа- и ракетостроении, поскольку только указанные технологии позволяют получить легкие, исключительно прочные и термостойкие детали конструкций. Поэтому-то разработчикам и удается создавать более совершенные модели самолетов и космических кораблей.
Но вернемся на землю. Посмотрим, насколько востребованы композиты, и карбон в том числе, в строительстве.
Армирование бетона
Использование арматуры нового типа для бетонных конструкций — одно из очевидных применений композитов в строительстве. Композитная арматура — это стержни из стеклянных, базальтовых, углеродных или арамидных волокон, пропитанных полимерным связующим и отвержденных. Тип использованного волокна определяет и характер полученной арматуры. Довольно распространены изделия с наполнителем из стекловолокна — стеклопластиковая арматура (АСП), из базальтовых волокон — базальтопластиковая (АБП), из углеродных волокон — углепластиковая. Для сцепления с бетоном на поверхности композитной арматуры в процессе производства формируются специальные ребра или наносится покрытие из песка.
Стальная арматура в железобетоне подвержена коррозии, а вот композитный материал в этом плане выгодно отличается от нее благодаря высокой коррозионной стойкости, особенно у базальтопластика. Однако и у базальтопластиковой, и у стеклопластиковой арматуры есть свои недостатки: низкий модуль упругости (примерно в 3-4 раза ниже, чем у стальной) и заметная потеря прочности при нагреве. Поэтому подобную композитную арматуру чаще используют в качестве гибких связей для трехслойных стен из кирпича и других штучных материалов или для соединения несущих железобетонных стен с кирпичной облицовкой и пр. с целью снижения теплопередачи ограждений.
В этом плане углепластиковая арматура имеет лучшие характеристики, чем стекло- и базальтопластика. Это абсолютная коррозионная стойкость (инертность ко всем агрессивным средам), высокая прочность, долговечность (ожидаемый срок службы — 75 лет), низкий вес. Использование углепластиковой арматуры позволяет изготавливать более длинные силовые секций в сборных конструкциях. Но и стоимость такого композита в разы больше, что, в общем-то, и ограничивает его применение.
Усиление конструкций
Одно из важных направлений использования углепластика — когда на поверхности балки, стойки и пр. с помощью специального клея фиксируют сверхпрочную углеткань. При этом обеспечивается повышение прочности элементов в растянутых зонах и приопорных участках в зоне действия поперечных сил, а также сжатых элементов. Так, в 2003 году углеродные ленты использовали для усиления балок пролетов автодорожного моста на 104-м км трассы Москва-Нижний Новгород.
Усиливать можно стальные, деревянные и даже каменные конструкции — столбы, пилоны, простенки. Также это могут быть кирпичные или бетонные стены, поврежденные после просадки фундамента, или ограждения с проемами (окнами, дверями, технологическими отверстиями). Натурные испытания кирпичных столбов, проведенные в лаборатории каменных конструкций ЦНИИСК в 2004 году, например, показали полутора-двукратное увеличение несущей способности кирпичных столбов, усиленных бандажами из углехолста.
Готовые изделия из композита
В строительстве полимерные композиты — это материалы для изготовления градирен, емкостей для транспортировки и хранения химически активных веществ, трубопроводы разного назначения, элементы конструкций мостов, ограждения на автодорогах, плавательные бассейны, передвижные домики, выставочные павильоны и многое другое.
Как видим, композиты имеют весьма широкую область применения, но если сравнивать Россию с промышленно развитыми странами, наши успехи пока скромны. Если до конца 80-х прошлого века в сфере разработки композитов мы шли с Западом нога в ногу, то после развала СССР наше развитие в этой области приостановилось. Между тем потребность в композитных материалах не уменьшается, а только возрастает. Но из-за крайне медленного развития собственного производства мы все больше и больше становимся зависимыми от импорта. Чтобы как-то уйти от этой зависимости, необходимо решить ряд проблем технического и организационного характера, требующих не только огромных средств, но и времени.
Прежде всего, необходимо создать условия для роста серийного производства углеродных композитов. Сегодня холдинговая компания «Композит» является единственным игроком, оказывающим влияние на развитие российского рынка углеродного волокна. А отсутствие конкуренции на рынке углеродного волокна не способствует ни снижению цены на него, ни росту объемов производства. Привлечь инвесторов в достаточно новую, наукоемкую сферу без быстрого возврата вложенных средств очень сложно — для этого нужны весомые рычаги. Можем ли мы своими силами изготовить необходимое оборудование или придется закупать дорогостоящие станки за рубежом? Это к вопросу об импортозамещении. Четкого ответа на этот вопрос пока нет.
Для производства новых композитов, их применения и эксплуатации изделий из них нужны квалифицированные специалисты. Их подготовка — часть большой комплексной работы. И пока мы с этим тянем, в правительстве обсуждается вопрос о том, что надо привлекать мигрантов, уже обученных у себя на родине.
На бумаге все гладко…
Существенно тормозит внедрение углеродных композитов затягивание процесса принятия нормативной документации, регламентирующей применение новых материалов, особенно в строительстве. Например, отсутствие СНиПов в области применения углеродных композитов ставит практически непроходимый барьер для проектов в Госстройэкспертизе.
Конечно, сам факт создания плана мероприятий «Развитие отрасли производства композитных материалов» намечает пути решения этих проблем, но при этом данной «дорожной картой» …не устанавливается направление бюджетных ассигнований на реализацию предусмотренных документом мероприятий».
Время покажет, как чиновники отрапортуют о решении поставленных задач. Не исключено, что это будет большой «бумажный» успех.
Подготовил Владислав ТИХОМИРОВ
Фото infuture.ru, mvtb.ru, nowing.ru, nanonewsnet.ru, avito.st
Особенности и преимущества карбона. Его недостатки и способы имитации • MonsterAuto.ru
Для многих автолюбителей желание тюнинговать свой автомобиль стало по-настоящему навязчивой идеей. Хочется изменить своего «железного коня», сделать его более ярким, непохожим на остальных. Так, одним из наиболее популярных направлений внешнего и внутреннего тюнинга является использование карбона. Но какой он этот материал, какие у него есть преимущества и недостатки, как его можно использовать. Давайте разберемся с этими вопросами более подробно.
Что такое карбон и чем он отличается от углепластика?
Производство столь популярного композитного материала было налажено уже давно. В начале 20 века, англичане из Фарнборо продемонстрировали публике первые детали, выполненные из этого чудо-материала. В его основе – огромное число переплетенных углеродных нитей, которые крепятся между собой с помощью эпоксидной смолы. Чтобы придать материалу максимальной прочности они укладываются под определенным углом друг к другу. Именно углеродные нити являются основным элементом этого композитного материала. Несмотря на свою минимальную толщину, их невозможно сломать или порвать. Рисунок современного стекловолокнистого полимера может быть выполнен в виде рогожи, елочки и прочих фигур.
Карбоновый задний диффузор
Карбон активно применяется во многих сферах жизни, но в тюнинге автомобилей больше всего. Из этого материала изготавливаются спойлеры, капоты, различные элементы салона и кузова. Если вы собрались строить сверхоблегченный корч, то использование этого углеродного материала просто необходимо. Кроме этого, карбон нашел свое применение не только в авто – его активно используют для производства основных деталей катеров, снегоходов, мотоциклов и других видов транспорта.
Карбоновый воздухозаборник
Преимущества и недостатки углепластика
Материал «карбон» достаточно специфичен по своей структуре и особенностям, поэтому у него есть, как положительные, так и отрицательные стороны. К основным преимуществам можно отнести легкость и прочность. Что касается прочности, то благодаря особому плетению нитей, этот композитный материал и вовсе не уступает многим современным металлам. Вес карбона почти вполовину меньше, чем у стали и на 1/5 меньше, чем у алюминия.
Карбоновая крыша автомобиля
Карбон: какая прочность на разрыв?
Слышали об уникальной прочности стекловолокна? Так вот, деталь, выполненная из карбона, обладает гораздо лучшими характеристиками в этом отношении. Поэтому именно этот композит применяется в автоспорте, где особое внимание уделяется безопасности пилотов и достижению результата. Любое снижение веса болида при сохранении максимального уровня прочности – это только плюс.
Дверь и капот
Насколько этот углепластик прочнее металла?
Но есть у карбона и явные недостатки. Многих любителей тюнинга от покупки углепластиковых элементов «отговаривает» высокая стоимость. Если сравнивать с тем же стекловолокном, то карбон намного дороже. В качестве причины можно привести как раз уникальную технологическую сложность процесса производства. Да и сами исходные материалы обходятся производителям в «копеечку». К примеру, склеивание различных слоев в материале осуществляется с помощью качественных и дорогих смол. Кроме того, компании-производители для выпуска карбона вынуждены закупать специализированное и дорогостоящее оборудование.
Задний спойлер
Но это не все недостатки популярного материала для тюнинга. Как показывает практика, этот композитный материал очень боится точечных и сильных ударов. Достаточно сильного воздействия даже мелкого камешка, чтобы насквозь пробить карбоновый элемент автомобиля. Уже через несколько лет эксплуатации тот же капот может иметь вид настоящего решета. Кроме этого, карбон очень не любит солнечных лучей. Если не прятать автомобиль в гараж и оставлять его на улице, то скоро первоначальный цвет будет утерян.
Каркас и растяжки
Мы уже упоминали о чувствительности этого композита к различным ударам. Так вот, при повреждении данный материал невозможно постановить. Единственным выходом для автолюбителя является только полная замена детали, а это, как вы уже поняли, серьезные затраты.
Капот из углеволокна
Возможна ли имитация карбона?
Обычному автолюбителю все равно, насколько прочным или легким является карбон. Главное, что он очень красиво смотрится – именно это привлекает любителей тюнинга. Поэтому нет необходимости использовать оригинальный дорогостоящий материал – достаточно его имитации.
Дверные ручки «под-карбон»
Пленки ПВХ
Сегодня можно имитировать карбон несколькими различными методами. Наибольшую популярность (именно по причине своей доступности) получила специальная карбоновая ПВХ пленка, дублирующая оригинальный рисунок. Подобных «заменителей» сегодня множество, в самом различном исполнении. С помощью строительного фена и пленки можно оклеить практически любую деталь интерьера и экстерьера автомобиля, придав ей необычный вид карбона. Конечно, обтянуть мелкие элементы с первого раза не всегда получается, но если потренироваться, то даже эта задача становится выполнимой. Если в работе все-таки возникают проблемы, то всегда можно обратиться к мастерам своего дела. Организаций, которые занимаются подобным видом тюнинга, сегодня достаточно.
Аквапечать
Второй вариант имитации карбона – так называемая аквапечать. Здесь также осуществляется обклейка специальной пленкой, но накладывается она под давлением воды. Сделать такую работу в «гаражных» условиях уже не получится – необходимо дополнительное оборудование. Преимущество такого метода заключается в более высоком качестве тюнинга. При этом пленку, в отличие от прошлого метода, можно наносить даже на самые «фигуристые» детали. Если обработка выполнена качественно и с соблюдением технологии, то внешний вид нисколько не будет отличаться от настоящего карбона.
К слову, формулировка «кузов или салон под карбон» сегодня очень популярна. Так вот, это совсем не значит, что элементы выполнены из дорогостоящего материала – просто сделана обтяжка специальной пленкой посредством одной из технологий, описанных выше.
Аэрография «под-карбон»
Раз мы уже начали описывать все варианты имитации, то должны упомянуть и третий способ – нанесение аэрографии. Конечно, по конечному внешнему виду данный метод хуже, чем два предыдущих, но в определенных кругах автолюбителей он также пользуется популярностью. Аэрограф, к сожалению, не способен с точностью передать рисунок композита – именно с этим и возникают определенные проблемы.
Как сэкономить на покупке и какова цена вопроса?
В любом случае композитный тюнинг сегодня очень популярен. Немного затрат и можно преобразить свой автомобиль, сделать его узнаваемым и ярким. кроме этого, карбоновая пленка, нанесенная на внешние элементы кузова, способна защитить металл и краску от внешних воздействий. Бесспорно, лучше использовать натуральный карбон или углепластиковый полимер. Но если необходимой суммы в наличии нет, то пленка «под-карбон» – лучший вариант.
Что такое карбон и его модульность?
«
Три крупнейших японских завода, производящие карбон: Toray, Mitsubishi и Toho
«
В настоящее время у производителей всех известных марок спиннингов обязательно присутствуют модельные ряды из карбона (углепластика, графита).

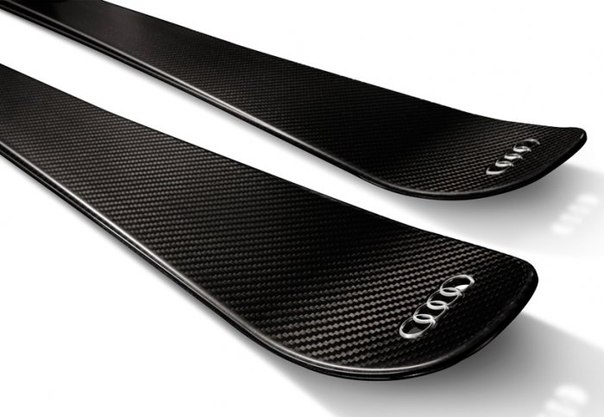
В заключение хочется добавить, что не стоит выбирать спиннинг только исходя из марки или модульности карбона, необходимо смотреть на строй, тест, ручку и насколько вам удобно будет ловить данным орудием.
Углеродные волокна: производство, свойства и возможности использования
Пуджа Бхатт и Алка Го
Старший научный сотрудник, профессор и руководитель отдела одежды и текстиля, G.B.P.U.A and T, Пантнагар
Автор, ответственный за переписку Электронная почта: [email protected]
DOI: http://dx.doi.org/10.13005/msri/140109
История публикации статьи
Статья получена: 30 мая 2017 г.
Статья принята: 5 июня 2017 г.
Статья опубликована: 9 июня 2017 г.
Проверка на плагиат: Да
Углеродное волокно состоит из атомов углерода, связанных вместе, образуя длинную цепочку.Волокна чрезвычайно жесткие, прочные и легкие и используются во многих процессах для создания превосходных строительных материалов. Углеродное волокно входит в состав множества «сырых» строительных блоков, включая пряжу, однонаправленную, переплетенную, тесьму и некоторые другие, которые, в свою очередь, используются для создания композитных деталей. Детали из углеродного волокна по своим свойствам близки к стальным, а по весу — к пластиковым. Таким образом, отношение прочности к весу (а также отношение жесткости к весу) детали из углеродного волокна намного выше, чем у стали или пластика.Углеродное волокно чрезвычайно прочное. В инженерии типично измерять преимущество материала с точки зрения отношения прочности к весу и отношения жесткости к весу, особенно при проектировании конструкций, где добавленный вес может привести к увеличению стоимости жизненного цикла или неудовлетворительным характеристикам.
Чтобы процитировать эту статью, скопируйте следующее: Bhatt P, Goe A. Углеродные волокна: производство, свойства и потенциальное использование.Математические науки и ресурсы Индии; 14 (1) |
Введение
Углеродные волокна или углеродные волокна — это волокна диаметром около 5–10 микрометров, состоящие в основном из атомов углерода. Углеродные волокна обладают рядом преимуществ, включая высокую жесткость, высокую прочность на разрыв, малый вес, высокую химическую стойкость, устойчивость к высоким температурам и низкое тепловое расширение. Эти свойства сделали углеродное волокно очень популярным в аэрокосмической отрасли, гражданском строительстве, военном деле и автоспорте, а также в других соревновательных видах спорта.Однако они относительно дороги по сравнению с аналогичными волокнами, такими как стекловолокно или пластмассовые волокна.
Классификация и виды
Углеродные волокна по модулю, прочности и конечной температуре термообработки можно разделить на следующие категории:
В зависимости от свойств углеродного волокна углеродные волокна можно сгруппировать в:
- Сверхвысокий модуль, тип UHM (модуль> 450 ГПа)
- Высокомодульный, тип HM (модуль упругости 350-450 ГПа)
- Промежуточный модуль, тип IM (модуль между 200-350 ГПа)
- Низкий модуль и высокий предел упругости, тип HT (модуль <100 ГПа, предел прочности> 3.0 ГПа)
- Сверхвысокопрочный, типа SHT (предел прочности на разрыв> 4,5 ГПа)
Углеродные волокна на основе материалов-предшественников подразделяются на:
- Углеродные волокна на основе ПАН
- Углеродные волокна на основе пека
- Углеродные волокна на основе мезофазного пека
- Углеродные волокна на основе изотропного пека
- Углеродные волокна на вискозной основе
- Углеродные волокна, выращенные в газовой фазе
Углеродные волокна по температуре окончательной термообработки подразделяются на:
- Углеродные волокна, подвергнутые высокой термообработке (HTT), тип I, где конечная температура термообработки должна быть выше 2000 ° C и может быть связана с волокном высокомодульного типа.
- Углеродные волокна с промежуточной термообработкой (IHT), тип II, где конечная температура термообработки должна быть около или выше 1500 ° C и может быть связана с волокном высокопрочного типа.
- Углеродное волокно с низкой термической обработкой, тип III, температура конечной термообработки которого не превышает 1000 ° C. Это низкомодульные и малопрочные материалы.
Производственный процесс
Углеродные волокна из полиакрилонитрила (PAN):
Сырье
Сырье, используемое для производства углеродного волокна, называется прекурсором.Около 90% производимых углеродных волокон состоит из полиакрилонитрила. Остальные 10% сделаны из искусственного шелка или нефтяного пека. Все эти материалы представляют собой органические полимеры, характеризующиеся длинными цепочками молекул, связанных вместе атомами углерода. Точный состав каждого прекурсора варьируется от одной компании к другой и обычно считается коммерческой тайной. В процессе производства используются различные газы и жидкости. Некоторые из этих материалов предназначены для взаимодействия с волокном для достижения определенного эффекта.Другие материалы предназначены для того, чтобы не вступать в реакцию или предотвращать определенные реакции с волокном. Как и в случае с прекурсорами, точный состав многих из этих технологических материалов считается коммерческой тайной.
Производственный процесс PAN
Рисунок 1
Прядильная
- Порошок акрилонитрильного пластика смешивают с другим пластиком, таким как метилакрилат или метилметакрилат, и подвергают взаимодействию с катализатором в обычном процессе суспензионной или растворной полимеризации с образованием полиакрилонитрильного пластика.
- Затем пластик превращается в волокна одним из нескольких различных методов. В некоторых методах пластик смешивается с определенными химическими веществами и закачивается через крошечные форсунки в химическую ванну или камеру закалки, где пластик коагулирует и затвердевает в волокна.
Это похоже на процесс, используемый для формирования полиакриловых текстильных волокон. В других методах пластиковая смесь нагревается и перекачивается через крошечные форсунки в камеру, где растворители испаряются, оставляя твердое волокно. Этап прядения важен, потому что во время этого процесса формируется внутренняя атомная структура волокна.
- Затем волокна промывают и растягивают до желаемого диаметра. Растяжение помогает выровнять молекулы внутри волокна и обеспечивает основу для образования прочно связанных кристаллов углерода после карбонизации.
Стабилизатор
Перед карбонизацией волокон их необходимо химически изменить, чтобы преобразовать их линейную атомную связь в более термически стабильную лестничную связь. Это достигается путем нагревания волокон на воздухе примерно до 390-590 ° F (200-300 ° C) в течение 30-120 минут.Это заставляет волокна улавливать молекулы кислорода из воздуха и изменять структуру их атомных связей. Стабилизирующие химические реакции сложны и включают несколько этапов, некоторые из которых происходят одновременно. Они также генерируют собственное тепло, которое необходимо контролировать, чтобы избежать перегрева волокон. В коммерческих целях для процесса стабилизации используется различное оборудование и методы. В некоторых процессах волокна протягиваются через ряд камер с подогревом. В других случаях волокна проходят через горячие валки и через слои сыпучих материалов, удерживаемых во взвешенном состоянии потоком горячего воздуха.В некоторых процессах используется нагретый воздух, смешанный с определенными газами, которые химически ускоряют стабилизацию.
Карбонизация
После того, как волокна стабилизируются, их нагревают до температуры примерно 1,830-5,500 ° F (1,000-3,000 ° C) в течение нескольких минут в печи, заполненной газовой смесью, не содержащей кислорода. Недостаток кислорода предотвращает сгорание волокон при очень высоких температурах. Давление газа внутри печи поддерживается выше, чем давление наружного воздуха, а точки входа и выхода волокон из печи герметизированы, чтобы не допустить попадания кислорода. Когда волокна нагреваются, они начинают терять свои неуглеродные атомы, а также несколько атомов углерода в виде различных газов, включая водяной пар, аммиак, монооксид углерода, диоксид углерода, водород, азот и другие. Когда неуглеродные атомы вытесняются, оставшиеся атомы углерода образуют прочно связанные углеродные кристаллы, которые ориентированы более или менее параллельно длинной оси волокна. В некоторых процессах используются две печи, работающие при двух разных температурах, чтобы лучше контролировать скорость разогрева во время карбонизации.
Рисунок 2
Обработка поверхности
После карбонизации волокна имеют поверхность, которая плохо сцепляется с эпоксидными смолами и другими материалами, используемыми в композитных материалах. Чтобы волокна лучше склеивали, их поверхность слегка окисляется. Добавление атомов кислорода к поверхности обеспечивает лучшие свойства химического связывания, а также травит и делает поверхность шероховатой для улучшения механических свойств связывания. Окисление может быть достигнуто путем погружения волокон в различные газы, такие как воздух, диоксид углерода или озон; или в различных жидкостях, таких как гипохлорит натрия или азотная кислота. На волокна также можно нанести электролитическое покрытие, сделав волокна положительным выводом в ванне, заполненной различными электропроводящими материалами. Процесс обработки поверхности необходимо тщательно контролировать, чтобы избежать образования крошечных дефектов поверхности, таких как ямки, которые могут вызвать повреждение волокна.
Калибровка
- После обработки поверхности волокна покрываются покрытием для защиты от повреждений при намотке или плетении.Этот процесс называется калибровкой. Материалы покрытия выбираются таким образом, чтобы они были совместимы с клеем, используемым для формирования композитных материалов. Типичные материалы покрытия включают эпоксидную смолу, полиэстер, нейлон, уретан и другие.
- 8 Волокна с покрытием наматываются на цилиндры, называемые бобинами.
Бобины загружаются в прядильную машину, и волокна скручиваются в пряжу различных размеров.
Недвижимость
Углеродное волокно имеет высокое отношение прочности к массе (также известное как удельная прочность)
Прочность материала — это сила, приходящаяся на единицу площади при разрушении, деленная на его плотность.Любой прочный И легкий материал имеет подходящее соотношение прочности и веса. Такие материалы, как алюминий, титан, магний, углерод и стекловолокно, высокопрочные стальные сплавы, имеют хорошее соотношение прочности к весу.
Углеродное волокно очень жесткое
Жесткость или жесткость материала измеряется его модулем Юнга и измеряет, насколько материал прогибается под действием напряжения. Пластик, армированный углеродным волокном, более чем в 4 раза жестче, чем пластик, армированный стекловолокном, почти в 20 раз больше, чем сосна, 2.В 5 раз больше алюминия.
Углеродное волокно устойчиво к коррозии и химически устойчиво
Хотя углеродное волокно само по себе не портится, эпоксидная смола чувствительна к солнечному свету и требует защиты. Другие матрицы (независимо от того, в какое углеродное волокно встроено) также могут быть реактивными.
Углеродное волокно электропроводное
Эта функция может быть полезной и неприятной. При строительстве лодок это необходимо учитывать, так как в игру вступает проводимость алюминия.Электропроводность углеродного волокна может способствовать гальванической коррозии арматуры. Тщательная установка может уменьшить эту проблему.
Усталостное сопротивление хорошее
Устойчивость к усталости композитов из углеродного волокна — хорошая. Однако, когда углеродное волокно выходит из строя, оно обычно катастрофически выходит из строя, и это не говорит о его неизбежном разрыве. Повреждение в результате усталости при растяжении рассматривается как снижение жесткости при увеличении количества циклов напряжения (если температура не высокая). Испытания показали, что разрушение вряд ли будет проблемой, когда циклические напряжения совпадают с ориентацией волокна. Углеродное волокно превосходит стекло E по усталостной и статической прочности, а также по жесткости.
Углеродное волокно имеет хорошую прочность на разрыв
Предел прочности на разрыв или предел прочности — это максимальное напряжение, которое может выдержать материал при растяжении или растяжении до образования шейки или разрушения. Сужение — это когда поперечное сечение образца начинает значительно сокращаться. Если вы возьмете полоску полиэтиленового пакета, она растянется и в какой-то момент начнет сужаться. Это шею.Он измеряется в силе на единицу площади. Хрупкие материалы, такие как углеродное волокно, не всегда выходят из строя при одном и том же уровне напряжения из-за внутренних дефектов. Они терпят неудачу при малых деформациях.
Испытание включает взятие образца с фиксированной площадью поперечного сечения, а затем его вытягивание, постепенно увеличивая силу, пока образец не изменит форму или не сломается. Волокна, такие как углеродные волокна, имеющие диаметр всего 2/10 000-х дюйма, превращаются в композиты соответствующей формы для испытаний.
Огнестойкость / негорючий
В зависимости от производственного процесса и материала-прекурсора углеродное волокно может быть довольно мягким и его можно использовать в качестве защитной одежды для пожарных или, что более часто, интегрировать в нее.Примером может служить волокно с никелевым покрытием. Поскольку углеродное волокно также химически очень инертно, его можно использовать там, где есть огонь в сочетании с коррозионными агентами. Carbon Fiber Fire Blanket извините за опечатки.
Теплопроводность углеродного волокна
Теплопроводность — это количество тепла, передаваемого через единицу толщины в направлении, перпендикулярном поверхности единицы площади, из-за единичного температурного градиента в установившихся условиях. Другими словами, это показатель того, насколько легко тепло проходит через материал.
Поскольку существует множество вариаций углеродного волокна, невозможно точно определить теплопроводность. Специальные типы углеродного волокна были специально разработаны для обеспечения высокой или низкой теплопроводности. Также предпринимаются попытки улучшить эту функцию.
Низкий коэффициент теплового расширения
Это мера того, насколько материал расширяется и сжимается при повышении или понижении температуры. Единицы измерения указаны в дюймах / дюймах градусах F. Как и в других таблицах, единицы измерения не так важны, как сравнение.При достаточно высокой мачте разница в коэффициентах теплового расширения различных материалов может немного изменить натяжение буровой установки. Низкий коэффициент теплового расширения делает углеродное волокно подходящим для применений, где малые движения могут быть критичными. Одно из таких приложений — телескоп и другое оптическое оборудование.
Неядовит, биологически инертен, проницаем для рентгеновских лучей
Эти качества делают углеродное волокно полезным в медицине. Использование протезов, имплантатов и восстановления сухожилий, рентгеновских принадлежностей, хирургических инструментов — все это находится в стадии разработки. Хотя углеродные волокна не ядовиты, они могут вызывать сильное раздражение, поэтому необходимо ограничить длительное незащищенное воздействие. Однако эпоксидная или полиэфирная матрица может быть токсичной, поэтому необходимо соблюдать осторожность.
Углеродное волокно относительно дорого
Несмотря на то, что он предлагает исключительные преимущества прочности, жесткости и снижения веса, его стоимость является сдерживающим фактором. Если преимущество в весе не является исключительно важным, например, в аэронавтике или гонках, оно часто не стоит дополнительных затрат.Дополнительным преимуществом является низкая потребность в обслуживании углеродного волокна.
Трудно количественно охарактеризовать круто и модно. Углеродное волокно имеет ауру и репутацию, которые заставляют потребителей платить больше за то, чтобы иметь его. Возможно, вам понадобится меньше его по сравнению со стекловолокном, и это может быть экономией.
Углеродные волокна хрупкие
Слои волокон образованы прочными ковалентными связями. Листовые агрегаты легко допускают распространение трещин.Когда волокна изгибаются, они выходят из строя при очень малой деформации.
Приложения
Характеристики и применение углеродных волокон
1. Физическая прочность, удельная вязкость, легкий вес | Авиакосмическая промышленность, автомобильный и морской транспорт, спортивные товары |
2. Высокая стабильность размеров, низкий коэффициент теплового расширения и низкий уровень абразивного износа | Ракеты, авиационные тормоза, аэрокосмическая антенна и опорная конструкция, большие телескопы, оптические стенды, волноводы для стабильных высокочастотных (ГГц) прецизионных измерительных рам |
3.Хорошее гашение вибрации, прочность и ударная вязкость | Аудиотехника, громкоговорители для Hi-Fi оборудования, звукосниматели, манипуляторы |
4. | Автомобильные капоты, новая оснастка, корпуса и основания для электронного оборудования, защита от электромагнитных и радиочастотных помех, щетки |
5. Биологическая инертность и рентгеновская проницаемость | Медицинское применение в протезах, хирургическом и рентгеновском оборудовании, имплантатах, восстановлении сухожилий / связок |
6.Усталостная прочность, самосмазывание, высокое демпфирование | Текстильное оборудование, общее машиностроение |
7. Химическая инертность, высокая коррозионная стойкость | Химическая промышленность; ядерное поле; клапаны, уплотнения и компоненты насосов на технологических установках |
8. Электромагнитные свойства | Большие стопорные кольца генератора, радиологическое оборудование |
Заключение
Последняя разработка в технологии углеродного волокна — это крошечные углеродные трубки, называемые нанотрубками.Эти полые трубки, некоторые из которых имеют диаметр 0,00004 дюйма (0,001 мм), обладают уникальными механическими и электрическими свойствами, которые могут быть полезны при создании новых высокопрочных волокон, субмикроскопических пробирок или, возможно, новых полупроводниковых материалов для интегральных схем.
Список литературы
- Франк Э., Херманутц Ф. и Бухмайзер М. Р. Углеродные волокна: прекурсоры, производство и свойства. Макромол. Mater. Eng . 2012; 297: 493–501.
CrossRef - Шаваллер Д., Клаус Б. и Бухмайзер М. Р. Керамические филаментные волокна — Обзор . Макромол . Mater. Eng . 2012: 297: 502–522.
CrossRef - Хо К., Цянь К. К. и Бисмарк Х. А. Углеродное волокно: свойства поверхности. Энциклопедия композитов Wiley . 2011; 1–11.
- Хуанг X. Изготовление и свойства углеродных волокон. Материалы. 2009; 2 : 2369-2403.
CrossRef - Баджадж П., Паливал Д. К., Гупта А. К. Влияние ионов металлов на структуру и свойства акриловых волокон. J. Appl. Polym. Sci. 1998; 67: 1647–1659.
CrossRef - Гудхью П. Дж., Кларк А. Дж., Бейли Дж. Э. Обзор производства и свойств углеродных волокон. Mater. Sci. Англ. 1975; 17: 3–30.
CrossRef
Это произведение находится под международной лицензией Creative Commons Attribution 4.0.
Что такое углеродное волокно? | DragonPlate
Углеродное волокно состоит из атомов углерода, связанных вместе, образуя длинную цепочку.Волокна чрезвычайно жесткие, прочные и легкие и используются во многих процессах для создания превосходных строительных материалов. Углеродный волокнистый материал входит в состав множества «сырых» строительных блоков, включая пряжу, однонаправленную, переплетенную, плетеную и ряд других, которые, в свою очередь, используются для создания деталей из углеродного волокна.
Внутри каждой из этих категорий есть множество подкатегорий, требующих дальнейшего уточнения. Например, различные типы переплетения углеродного волокна приводят к различным свойствам композитной детали как при изготовлении, так и в конечном продукте.Чтобы создать композитную деталь, углеродные волокна, которые жесткие при растяжении и сжатии, нуждаются в стабильной матрице, чтобы оставаться в ней и сохранять свою форму. Эпоксидная смола — это превосходный пластик с хорошими характеристиками сжатия и сдвига, который часто используется для формирования этой матрицы, при этом углеродные волокна обеспечивают армирование. Поскольку эпоксидная смола имеет низкую плотность, можно создать легкую, но очень прочную деталь. При изготовлении композитной детали можно использовать множество различных процессов, включая мокрую укладку, вакуумную упаковку, перенос смолы, согласованные инструменты, формование со вставкой, пултрузию и многие другие методы.Кроме того, выбор смолы позволяет адаптировать ее к конкретным свойствам.
Углеродные волокна, армирующие стабильную эпоксидную матрицу
Прочность, жесткость и сравнение с другими материалами
Углеродное волокно чрезвычайно прочно. В инженерии типично измерять преимущество материала с точки зрения отношения прочности к весу и отношения жесткости к весу, особенно при проектировании конструкций, где добавленный вес может привести к увеличению стоимости жизненного цикла или неудовлетворительным характеристикам.Жесткость материала измеряется его модулем упругости. Модуль упругости углеродного волокна обычно составляет 33 мси (228 ГПа), а его предел прочности на разрыв обычно составляет 500 фунтов на квадратный дюйм (3,5 ГПа). Материалы из углеродного волокна с высокой жесткостью и прочностью также доступны благодаря специальным процессам термообработки с гораздо более высокими значениями. Сравните это с 2024-T3 Aluminium, который имеет модуль упругости всего 10 msi и предел прочности на разрыв 65 ksi, и 4130 Steel, который имеет модуль упругости 30 msi и предел прочности на растяжение 125 ksi.
Сталь будет постоянно деформироваться при уровне напряжения ниже ее предела прочности на растяжение. Уровень напряжения, при котором это происходит, называется пределом текучести. Углеродное волокно, с другой стороны, не будет постоянно деформироваться ниже своего предела прочности на разрыв, поэтому оно фактически не имеет предела текучести.
В качестве примера, ламинат, армированный углеродным волокном с полотняным переплетением, имеет модуль упругости приблизительно 6 мси и объемную плотность приблизительно 83 фунта / фут 3 . Таким образом, весовая жесткость этого материала составляет 107 футов.Для сравнения, плотность алюминия составляет 169 фунтов / фут 3 , что дает жесткость к весу 8,5 x 106 футов, а плотность стали 4130 составляет 489 фунтов / фут 3 , что дает жесткость к весу 8,8 x 106 футов. Следовательно, даже основная панель из углеродного волокна с полотняным переплетением имеет отношение жесткости к весу на 18% больше, чем у алюминия, и на 14% больше, чем у стали. Использование препрега, в частности высокомодульных и сверхвысокомодульных препрегов из углеродного волокна, дает значительно более высокое соотношение жесткости к массе.Например, панель, содержащая слой из углеродного волокна со стандартным модулем упругости препрега 0/90, будет иметь модуль упругости примерно 8 мсек, или примерно на 30% жестче, чем варианты без препрега. Для очень требовательных приложений, где требуется максимальная жесткость, можно использовать сверхвысокомодульное углеродное волокно 110 м / кв. Это специализированное углеродное волокно на основе пека имеет жесткость на изгиб более чем в 3 раза по сравнению со стандартной панелью из препрега с модулем упругости (около 25 мсек). Если учесть возможность индивидуальной жесткости панели из углеродного волокна за счет стратегического размещения ламината, панель (или другое поперечное сечение, например труба) может быть изготовлена с жесткостью на изгиб порядка 50 мси.
Испытания, проведенные Dragonplate, показали, что все образцы однонаправленных сверхвысокомодульных образцов с нулевой ориентацией имеют жесткость на растяжение, превышающую 75 мсю, или более чем в два раза жесткость стали, но все же только половину веса алюминия. Если использовать вышеупомянутое сравнение, то отношение жесткости к весу этого материала более чем в 10 раз больше, чем у стали или алюминия. Если учесть потенциально значительное увеличение как прочности к весу, так и отношения жесткости к весу, которое возможно, когда эти материалы сочетаются с легкими сотами и вспененными сердцевинами, очевидно ли, какое влияние современные композиты из углеродного волокна могут оказать в самых разных областях применения.
Что такое композитная многослойная структура?
Композитный сэндвич сочетает в себе превосходные характеристики прочности и жесткости углеродного волокна с материалом сердцевины меньшей плотности. В случае сэндвич-листов Dragonplate углеродное волокно создает тонкий слой ламината на пенопласте, сотах, бальзе или березовой фанере. Стратегически комбинируя эти материалы, можно создать конечный продукт с гораздо более высоким соотношением жесткости к весу, чем с любым из них по отдельности. Для применений, где вес имеет решающее значение, сэндвич-листы из углеродного волокна могут подойти.
Композитная многослойная конструкция механически эквивалентна конструкции из однородной двутавровой балки при изгибе.
Рис. 1: Схема, показывающая многослойную конструкцию из углеродного волокна и эквивалентную двутавровую балку
На изображении многослойной конструкции в центре балки (при условии симметрии) находится нейтральная ось, где находится внутреннее осевое напряжение. равно нулю. Двигаясь снизу вверх на диаграмме, внутренние напряжения переключаются с сжатия на растяжение.Жесткость на изгиб пропорциональна моменту инерции поперечного сечения, а также модулю упругости материала. Таким образом, для максимальной жесткости на изгиб следует размещать чрезвычайно жесткий материал как можно дальше от нейтральной оси. Путем размещения углеродного волокна как можно дальше от нейтральной оси и заполнения оставшегося объема материалом с более низкой плотностью в результате получается композитный многослойный материал с высоким отношением жесткости к весу.
Рис. 2: Сравнение распределения внутренних напряжений для сплошного ламината и многослойной конструкции при изгибе.
Анализы FEA, сравнивающие многослойный ламинат с твердым углеродным волокном, показаны ниже. Эти расчеты показывают прогиб консольной балки с нагрузкой на конец. На рисунке показан слой сердцевины из березовой фанеры толщиной 3/16 дюйма рядом со слоем твердого углеродного волокна равного веса. Из-за уменьшенной толщины твердой углеродной балки она отклоняется значительно больше, чем эквивалентная балка, изготовленная из материала сердцевины. По мере увеличения толщины это несоответствие становится еще больше из-за значительной экономии веса сердечника.Точно так же можно заменить твердую углеродную структуру на более легкую, эквивалентную прочности и жесткости, сделанную из любого из ранее упомянутых вариантов сердечника.
Рис. 3: Сравнение анализа методом конечных элементов между многослойным слоистым материалом Dragonplate и твердым углеродным волокном
При использовании различных сердцевин каждый имеет свои сильные и слабые стороны. Обычно движущими факторами являются прочность сердечника на сжатие и сдвиг. Например, если требуется высокая прочность на сжатие (и, следовательно, высокое сопротивление раздавливанию), то сердцевина, скорее всего, должна быть более высокой плотности (здесь хорошими вариантами являются пенопласт высокой плотности или березовая фанера).Если, однако, нужен композит с абсолютно наименьшим возможным весом, а напряжения относительно малы (т. Е. Низкая нагрузка, высокая жесткость), то лучшим выбором может быть чрезвычайно легкий пенопласт или сотовый заполнитель. Некоторые сердечники обладают лучшей влагостойкостью (пенопласт с закрытыми порами), некоторые — лучшей обрабатываемостью (фанера), а другие — высоким отношением прочности на сжатие к весу (бальза). Задача инженера — понять компромиссы в процессе проектирования, чтобы максимально использовать потенциал композитных материалов с сердечником.Тем не менее, для критичных по весу приложений часто нет другого варианта, который хотя бы приблизился к потенциальной прочности и соотношению жесткости к весу ламинатов с многослойным сердечником из углеродного волокна.
КРИТЕРИИ СРАВНЕНИЯ | |||||||||||
ПРОДУКТЫ | Жесткость к весу | Прочность | Измельчение | Влагопоглощение | Влагопоглощение 9002 | Влагопоглощение Влагопоглощение | ЛУЧШЕ | ЛУЧШЕЕ | ЛУЧШЕ | ПЛОХО | |
Твердое углеродное волокно с высоким модулем упругости | ЛУЧШЕ | ХОРОШО | ЛУЧШЕ | ЛУЧШЕ | СЛАБЫЕ | ||||||
ЛУЧШЕЕ | 9050 ЛУЧШЕ | 9050 | ХОРОШО | ПЛОХО | |||||||
Бальзовое ядро | ЛУЧШЕ | ХОРОШО | ЛУЧШЕ | ПЛОХО | ХОРОШО | ||||||
Nomex Honeycomb Core | ЛУЧШЕ | ХОРОШЕЕ | ЛУЧШЕ | ЛУЧШЕ | |||||||
Depron Foam Core | ЛУЧШЕ | Плохо | Плохо | ЛУЧШЕ | ЛУЧШЕ | ||||||
Airex Foam Core | BEST | GOOD | GOOD | ЛУЧШЕ | ЛУЧШЕ | ЛУЧШЕЛУЧШЕ | ЛУЧШЕ | ЛУЧШЕ | ХОРОШО | ||
Last-A-Foam Core | ЛУЧШЕ | ЛУЧШЕ | ЛУЧШЕ | ЛУЧШЕ | ЛУЧШЕ | Углеродное волокно | Армированные композиты обладают несколькими очень желательными характеристиками, которые можно использовать при разработке современных материалов и систем.Два наиболее распространенных применения углеродного волокна — это приложения, в которых желательны высокая прочность по отношению к весу и высокая жесткость по отношению к весу. К ним относятся аэрокосмическая промышленность, военные структуры, робототехника, ветряные турбины, производственное оборудование, спортивный инвентарь и многие другие. Высокая прочность может быть достигнута в сочетании с другими материалами. В некоторых приложениях также используется электрическая проводимость углеродного волокна, а также высокая теплопроводность в случае специального углеродного волокна. Наконец, в дополнение к основным механическим свойствам углеродное волокно создает уникальную и красивую поверхность.